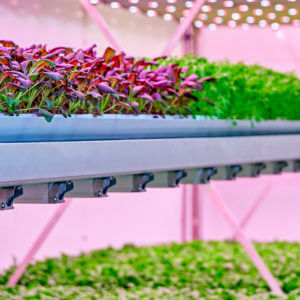
Quarantamila confezioni di insalate per la quarta gamma prodotte ogni giorno, pronte per essere distribuite nei supermercati milanesi. E poi, atmosfera controllata in maniera artificiale. Umidità, temperatura e concentrazione di anidride carbonica modulate per consentire alle piante di produrre al meglio. Luci a led per illuminare i vegetali e fertirrigazione per nutrirli e utilizzo di sensoristica avanzata.
La nuova frontiera dell’abbraccio fra innovazione tecnologica e agricoltura si chiama vertical farming e un progetto importante è rappresentato da Planet Farms: impianto in via di creazione alle porte di Milano, a Cavenago (Monza e Brianza); in prospettiva, una delle realtà più grandi d’Europa nel suo genere.
Promosso e ideato da Luca Travaglini e Daniele Benatoff, Planet Farms sarà la “culla” di migliaia di piante di taglia bassa e ciclo breve, come previsto dai vertical farm, nutrite con fertirrigazione a substrato di torba.
Impianti sostenibili con grande attenzione alle risorse come l’acqua
Le verticali farm sono realtà dislocabili ovunque, senza preoccupazioni in termini di costi per la logistica e il trasporto tipici delle coltivazioni in pieno campo. Hanno il grande vantaggio di rendere superflui gli agrofarmaci, dal momento che microrganismi patogeni, insetti e semi di malerbe non possono entrare nell’impianto.
E soprattutto, si tratta di strutture altamente sostenibili. Se produrre un chilo di lattuga in pieno campo richiede l’utilizzo di circa decine di litri di acqua, in una vertical farm ne basta una quantità molto inferiore.
Le verticali farm hanno peraltro costi di realizzazione importanti che nello stesso tempo, a regime, permettono ingenti quantità di energia per l’illuminazione, la climatizzazione e l’operatività degli impianti.
Processo automatizzato e sicurezza
La grande novità di una realtà come questa, rispetto ai metodi di agricoltura tradizionale, sta nel fatto che tutto deve essere sterilizzato, per evitare che si sviluppino microganismi patogeni. In altre parole, la torba viene attentamente controllata, l’aria filtrata e l’acqua sterilizzata con raggi ultravioletti.
Tutto il processo è meccanizzato: ci sono sistemi che si occupano del riempimento delle vasche con il substrato e del posizionamento dei semi e poi nastri trasportatori e carrelli elevatori che movimentano le vasche dentro e fuori le camere di germinazione e di crescita. Oltre a macchine che si occupano del taglio e del confezionamento delle verdure.
Morale: nessuno, prima del consumatore finale, tocca con mano l’insalata che esce dalla vertical farm. Cosa che, di questi tempi, gioca certamente a vantaggio della piena soddisfazione della clientela.